Tungsten Carbide Material
Tungsten carbide is a compound of tungsten and carbide that creates an extremely dense crystalline structure called hexagonal crystals. It is press-formed by a technique known as sintering. The sintered and manufactured carbide has compressive strength, extremely high thermal hardness, as called Solid carbide, with wear resistance, corrosion resistance and impact resistance.
Solid carbide refers to metal carbides. Fine grains of tungsten carbide are combined or cemented with cobalt. Powder metallurgy technology is cleverly used to produce solid carbide.
Tungsten carbide is often called carbide because of its extraordinarily high hardness relative to other metals. There are currently more than 20 different grades of tungsten carbide with varying grain size, hardness, tensile strength and melting point characteristics. Tungsten carbide is comparable to diamond as the hardest material available. It is used in major industries around the world and is widely used in machining applications requiring excellent wear resistance or impact resistance, such as in the manufacture of cutting and wear tools, molds and wear-resistant machine parts.

Minimum Transverse Fracture Strength (TRS), TRS is a measure of the strength of tungsten carbide that increases with cobalt content.
Tungsten carbide is one of the few materials that can be considered for machining jobs in industry, with excellent machinability and thermal properties and is extremely hard with a melting point in excess of 1800°C. End mills made from cemented tungsten carbide are highly wear-resistant and can withstand higher temperatures than ordinary high-speed steel (HSS) tools. Its hardness is close to diamond and it is mainly used to produce workpieces that are resistant to high pressure and high temperature.
Carbide cutting is typically used to machine carbon steel and stainless steel workpieces. Compared with steel workpieces, carbide cutting tools can provide a better finish on the parts because of their high sharpness, high temperature resistance, and increased machining speed. Tungsten carbide end mills make the drilling, grinding and milling of metals more efficient and economical.
Type of Solid Carbide Material | WC % |
CO % |
Average Grain Size/ µm |
GPA T.R.S. N/mm2 |
Desity ISO 3369 [g/cm3] |
Hardness Vickers HV30 | Coating | Working Material's Hardness |
---|---|---|---|---|---|---|---|---|
A | 90 | 10 | 0.6 | 3600 | 14.5 | 1600 | X-CEED![]() |
HRC 55 |
B | 86.65 | 13 | 0.4 | 3900 | 13.9 | 1700 | X-CEED![]() |
HRC 60 |
C | 89.8 | 9 | 0.2 | 4000 | 14.3 | 2000 | NACO![]() |
HRC 68 |
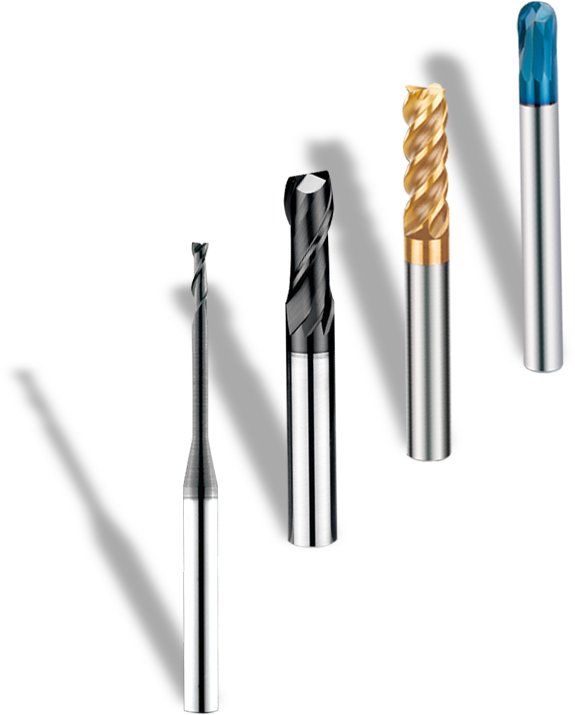